Does anybody have any suggestions for acoustical underlay for the floor? I need a dirt-cheap solution to somewhat de-couple the floor without putting another floor on top. Can strips of acoustical underlay mat be put between the floor and the joists? Currently, the plan is to just have Roxul safe n sound between the joists, but based on previous info that you guys have given me, I don’t think that will be enough.
I can’t say I have a dirt cheap solution. However, I am not sure I fully understand what you are asking. You said you are having floor joists on screw piles into the ground. so that means the floor will be suspended directly over the ground. So you are not pouring a concrete floor?
If what I said is correct your issue is going to be your floor acting like a drum. It is actually the worst possible way to deal with your floor as it will amplify any vibration. The best way to alleviate this drum effect is to fill the void between the floor joists with sand. It will add mass and dampen vibration significantly. But it doesn’t sound like this is a possibility based on the info above. If you are not using a full poured concrete floor this is going to compromise anything else you do as far as sound attenuation. Give me more details as to what you are doing, plans and maybe we can find a workable solution for you.
1 Like
Due to a steel gas line that can’t be moved, the building has to be a minimum of 1" above the ground, ruining the plan of a cement floor. I have put screw piles about 1 foot below the ground, 4 down each long side of the building (30’). On top of those screw piles, partly below and partly above the ground, are thick hardwood beams that run the 30’ sides of the building. On top of the beams, spanning the 22’ width of the building are 16" I-Joists to make the floor joists to be boarded. This leaves both ends of the building open to allow the air space under it to meet code for the gas line underground. Unfortunately, this was the only available option to meet building code, so I have to work with it. My contractor has assured me that there will be absolutely no bounce in the floor and it will be rock solid.
The plan for finishing was to use roxul safe n sound between the joists and carpet the floor to try and dampen the vibrations.
The walls are being constructed using the double leaf (resilient clips) method. The room will have a significant amount of absorption and diffusion inside, some removable if necessary.
And instead of the wooden construct, can’t you use something like this ?
You can also make it floating on your pillars if you just keep your vertical beams (brown lines) there, and use these concrete one’s to make the horizontal ones. (the green lines in this case)
After that its just a layer of concrete, and you have a nice floor. Its a pretty easy DIY thing, if you have them delivered, they can put them in place right away, and then its just a matter of making concrete, or having it delivered.
Depending on what you’re going to make your walls from, you can make iron wired bars into the concrete to attach your walls to.
I strongly recommend something like this, cause like @bobbybovine said you’re going to have a drum effect. You’re contractor can say what he want, but most construction builders don’t have a clue when it comes to sound. If you walk on it, it will be pretty sturdy of course, but waves are a hard thing to deal with.
Check out the book “construct it like the pro’s” There’s stuff about this exact situation. This will cost a little bit more, but you’re not going to be sorry about it ! If you really want to save all the bits of cash you can, you can also make those beams yourself, I can show you a plan, but that’s going to be very labour intensive 
1 Like
The material isn’t an option at this point. The building inspector mandated what the floor had to be, and it was purchased. I wanted to do cement originally, but because of the gas line, this was my only option. I can do simple changes like add insulation or try some kind of isolation, but that’s about it. Also keep in mind that, I don’t make any money at this. It’s a hobby studio for my band to mostly just practice in, so I have to keep things very economical and make the best of what I have. Basically looking for ways to isolate the floor as described the best that I can.
1 Like
Ah ok
Is it because it has to be easily deconstructable to get to the pipeline or ?
And if its mainly to rehearse with the band I guess you can fix it with some filling indeed. Was that sand idea an option ? If you have a double floor, I guess you can fill the floor with sand, and still keep the space between the ground and the floor.
The building basically has to be movable like a shed and have air space under it to prevent a gas build up in case of a leak.
As far as sand, I don’t see why I couldn’t put some in there. There has to be insulation put in under the floor boards, but under that i could put a layer of poly, then a layer of sand. How thick of a sand layer would you suggest? With the I-Joists spanning 22 feet, I will have to see how much extra weight we are allowed to put in there.
also, specifically sand? Would something like A-Base work as well?
Well I’m not really an “expert”, so that sand thing was more like a filler. I guess that if you have the floor filled with it, you come as close as you can to a concrete floor. I’m not sure if this is the best solution for you of course. I think the best thing to focus on, is that you make sure that the floor plates have as little as possible space to vibrate. Maybe just put a bit more isolation in it, and really press it together ?
1 Like
I guess, I will just do everything I can to add mass to the floor and limit vibration. I may be able to get a hold of some heavy rubber mat to go under the carpet, and I think the sand is do-able.
Has anybody ever tried one of those DIY tennis ball drum risers? I just found that online and thought that it might be a cheap solution to help with with drums and bass amps creating vibrations directly on the floor.
I am not an expert but I would look at the book “Build It Like The Pros” Ethan Winer recommended it to me and it was a HUGE help in my studio build.
3 Likes
Another one just watching with interest from the sidelines… good luck! 
2 Likes
Regarding using sand. This is not something you can do haphazardly, it will add significant weight to the structure and would have to be adjusted by the engineer in the plans to support that weight. So definitely DON’T do it without proper consultation. I have seen it used but in a subfloor that was built on top of a concrete slab with the joist of the floors on rubber pucks to isolate from the concrete sand filling the void. It worked extremely well. But in your situation likely would be cost prohibitive as well as possible building code issues.
Unfortunately your options are limited. Filling that cavity with Roxul safe and sound will help, cross bracing (blocking) the joists to prevent bounce in the floor will help and won’t cost a lot extra. Adding some sound isolation mat under the carpeting will also help (but definitely not cheap). Something else to consider is a product like Green Glue (http://www.greengluecompany.com)
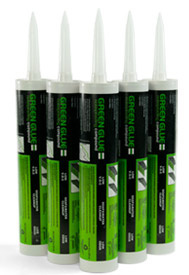
which you use between layers of plywood (or other flooring) will help with dampening the sound vibration (also possibly cost prohibitive).
All of these will help but you can only go so far in dealing with the floor suspended. Airborne vibration will mitigated mostly by what I explained above, it’s the flanking vibration (from amps, drums, jumping, stomping feet etc.) that will transmit through the floor the most. An isolated drum riser, getting amps of the floor on stands with a small footprint on some vibration barrier etc. will help with that to a degree.
Also follow Paul’s advice and read that book, and the books I mentioned earlier, it’s a lot to absorb especially if you are more interested in making music than learning about acoustics, but I hope you get something out of this that is satisfactory for your application.
Keep us all posted on your progress.
1 Like
Has anybody ever tried one of those DIY tennis ball drum risers? I just found that online and thought that it might be a cheap solution to help with with drums and bass amps creating vibrations directly on the floor.
Anything that creates some isolation is good. A tennis ball is flexible so it would likely do fairly well to build a platform on. I’ve not tried it myself.
1 Like
I’m waiting for some info back on the sand. to add a couple inches inside the floor will be like 7500-10000 pounds of extra weight. The Green Glue is a product that I am probably going to use. I was wondering specifically if it would help to put some between the joists and the floor boards to decouple it a bit. It would be a lot cheaper than putting it between two layers of floor boards.
I have been reading through those books. Some of the stuff about room modes and mixing makes sense because I deal with it in my current space. Since I don’t fully understand all of it, I am finding it difficult to decide on room size. The building is 22’x30’ (exterior dimensions) with 10’ walls. The interior dimensions will end up being about 20x28 with a 9’9" ceiling. Because of how my band and friends use the space, we have to go against the best acoustic advice and split it into a live room, mixing/lounging room, and a storage closet. I am trying to figure out the dimensions of all 3 for the best possible results. I will get a basic layout posted soon and would be open to suggestions.
I find this interesting, but don’t really understand it: http://amroc.andymel.eu/
The mixing room has to be big enough for a large couch and chair, small fridge, desk, a couple racks, office chairs, etc. The storage room needs to house about a dozen guitar cases, drum set, cables, stands, etc. and still be accessible. Biggest thing for us is space while we are playing, so the large size of the live room is high priority. Also, the original plan was to have the wall across on an angle, but I read that could cause issues in one of the books…
That is a LOT of extra weight, which might not be worth it. The green glue doesn’t decouple. It converts sound energy to heat energy and only works when the entire surface is covered. Using it on the joists only will have 0 effect and be a waste. There are recommendations on their website as to different amounts they recommend you use and the effectiveness of it.
With regards to room modes remember that these are based on ALL of the sound being reflected back into the room. Since you don’t have a solid concrete or brick walled room they aren’t going to be 100% accurate. That being said it is a good place to start. Do the best you can in regards to using them but there will always be compromises. Also room modes generally are most important regarding low frequencies that can’t easily be absorbed with acoustic treatment. I had a conversation with a FRAIC certified Acoustical Architect about treating low end in a non ideal room (room dimensions being (11’ x 22’) I said I wanted to use 3’ (36") depth of roxul on the back wall to eliminate low end reflections, and the room modes. He agreed that was likely the most cost effective way to deal with that situation and would yield very acceptable results which it did. Sometimes if you have the interior space you can deal with it by using copious treatment. Using ideal ratios will let you use less treatment overall. It’s all compromise. For mixing rooms symmetry is the most important consideration.
1 Like
Symmetry in the mixing room should be easy enough to accomplish, and room treatments are something that I actually have a decent handle on. Roxul is my friend.
1 Like
All done! The space is used about 75% for practice and 25% for recording. We did a practice run recording some drums on Monday, and the drums sound great! I’m very happy with the sound of the room. It could have been made a little bit more sound-proof to the outside, but I had to make some cutbacks due to budget. The outside walls are filled with fiberglass insulation inside a 16" stud wall (outside is plywood sheeting, vapor barrier, and vinyl siding), and inside is resilient channel covered in 5/8" drywall. Ceiling is the same. Floor is double layered with green glue in between the layers, fiberglass insulation between the joists and sand added for weight. A lot of sound escapes through the air conditioner vent pipe in the live room, but that was expected. A ductless system wasn’t in the budget.
For the recording end of things, I don’t have anything really expensive, but it works. I am running a MOTU 896 as my main 8-channel input with an M-Audio Octane for an additional 8 if needed. It’s hooked to a fairly high end computer (i7 quad core with 16gigs of ram, Glyph external HD) with ADAT and Firewire through an aftermarket sound card that i can’t remember the name of, and 2 computer monitors. The monitor on the desk is a 10 point touch screen that will sit flat and gets used as a mix console. The monitoring system is the next upgrade, but it does the trick for now.
Overall, it’s a really comfortable place for my band to hang out and have some fun. Well worth the investment!
2 Likes